Digitale Lagerverwaltung
Hochautomatisiert Ein- und Auslagern
Im italienischen Bozen läuft ein hochautomatisiertes Lagersystem fünfeinhalb Tage pro Woche rund um die Uhr, entlastet das Personal und gleicht einen möglichen Fachkräftemangel aus. Geplant und umgesetzt hat es das Team von Westfalia Technologies für Mila – Bergmilch Südtirol. Das kompakte automatische Satellitenlager ist an die Verarbeitung von jährlich mehr als 200.000 Tonnen Milch angebunden. Ein zentraler Förderstrang im Frischelager transportiert die Waren von der Produktion ins Lager und in die Kommissionierhallen. Das Frischelager ist rund 44 Meter lang, etwa 23 Meter breit und beherbergt bei einer Höhe von 17 Metern jeweils acht Ebenen mit bis zu vierfachtiefen Lagerkanälen und rund 4.140 Stellplätzen. Ketten-Satelliten sind für die Dreifach-Schienen im Einsatz. Sie lagern stündlich 65 Paletten im Doppelspiel und 62 Paletten im Einzelspiel. Ebenfalls in Betrieb sind zwei insgesamt 20 Meter lange seitliche Auslagerbahnen zwischen Kühllager und Kommissionierhallen.
Verwaltung von Stellplätzen, Bestand und Lager
Doch nicht nur anlagentechnisch, auch softwareseitig hat Westfalia Technologies das automatische Lagersystem auf den aktuellen technologischen Stand gebracht: „Mila hatte als langjähriger Kunde seit 1994 alle vier Generationen unserer Software im Einsatz, angefangen mit einem einfachen Lagerverwaltungssystem“, erklärt Christian Goltermann, Vertriebsleiter Software & IT. „Heute ist Savanna.NET zum Warehouse Execution System gewachsen, das Lagerverwaltung und Materialflusssteuerung vereint. Nach den Savanna-Upgrades auf Version 2.15 haben wir parallel zu den Bauabschnitten funktionale Erweiterungen implementiert.“ Dazu gehören die Verwaltung von Stellplätzen, Bestand und Lager, die Materialflusssteuerung, die Kopplung mit dem ERP-System SAP und die Bestandsbuchung über mobile Datenendgeräte auf der responsiven Bedienoberfläche. „Wir haben den Funktionsumfang um manuelle Lagerplätze in der neuen Kommissionierung, eine automatische Nachversorgung aus dem Hochregallager und die Stellplatzverwaltung der beiden Kommissionierzonen mittels mobilen Terminals erweitert“, so Goltermann.
Einlager- und Auslagerlogik reduzieren Umlagerungen und schöpfen die Lagerkapazität optimal aus. Die Scannerkommunikation hat das IT-Team von einer seriellen Verbindung auf eine TCP/IP-Netzwerkverbindung umgestellt, die Schnittstellen zu den neuen Regalbediengeräten und die erweiterte Fördertechnik softwareseitig implementiert. Ein Microsoft SQL Server ist als zentrale Datenbank eingerichtet. „Dank Savanna kommissionieren wir in den neuen Kommissionierzonen per Handheld und geben dezentral Anweisungen an das System“, fasst Thomas Bernhart, technischer Direktor von Mila – Bergmilch Südtirol, die Vorteile der Modernisierung zusammen.
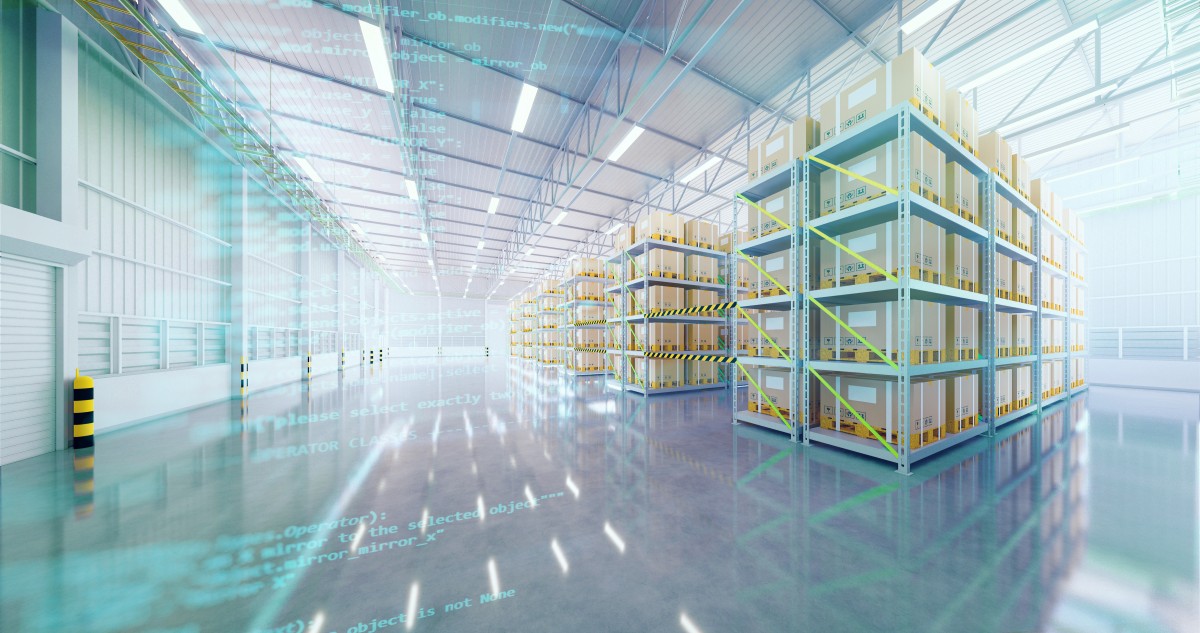
© SSI Schäfer TGmbH & Co KG
Mehr Intelligenz auf operativer Ebene
Das Beispiel zeigt: Um die Anforderungen in der Lebensmittelindustrie zu meistern, machen sich die Spezialisten für die Intralogistik das volle Potenzial softwarebasierter Systeme zunutze. Wo die klassische Lagerverwaltung durch ein Warehouse Management System (WMS) nicht mehr ausreicht, kommt ein Warehouse Execution System (WES) ins Spiel – als operative Intelligenz vermittelt es zwischen Systemsteuerung und Auftragsmanagement und fungiert als Bindeglied zwischen einem WMS und der Materialflusssteuerung. Echtzeitfunktionen zum Verwalten des Bestandes und zur Steuerung der Regalbediengeräte und Förderelemente im gesamten Lager zählen hier zu den zentralen Trends, die sich 2027 auch auf der Anuga FoodTec widerspiegeln. Auch lässt sich mit den in Köln gezeigten Lösungen jederzeit in den Materialfluss eingreifen, mit Maschinendaten Anlagen und Gerätezustände diagnostizieren und beliebig viele Lager zentral verwalten, steuern und synchronisieren.
Schnelle Digitalisierung für KMU
Eine konsequente Optimierung aller Prozesse und Komponenten als wichtiger Schritt in Richtung Intralogistik 4.0 – das will auch SSI Schäfer bieten. Mit den WAMAS Entry-Level Solutions richtet sich der Intralogistikspezialist an kleine und mittlere Unternehmen (KMU) sowie an Projekte mit mittlerem Komplexitätsgrad. Das Software-Portfolio bietet eine standardisierte, schnell implementierbare Möglichkeit, Lagerprozesse zu digitalisieren und zu automatisieren – und das bei hoher Skalierbarkeit. „Unser Ziel ist es, einen einfachen und schnellen Zugang zu modernster Lagersoftware zu schaffen, die auch mit den zukünftigen Anforderungen unserer Kunden mitwachsen kann. Dadurch profitieren Unternehmen von einer Lösung, die ihr Wachstum aktiv begleitet,“ so Florian Schneebauer, Vice President Product Line Software bei SSI Schäfer. Zum Angebot zählen die praxiserprobten Softwaremodule WAMAS Core WMS, eine Einstiegslösung für die digitale Lagerverwaltung, und WAMAS High Bay MFS, das automatisierte Hochregallager steuert.
Mit der Gründung von SupplyBrain erweitert SSI Schäfer zudem seine Digitalisierungskompetenz. Das Startup entwickelt datengestützte Softwarelösungen, die die Kernbereiche der Supply Chain adressieren. Mithilfe eines digitalen Zwillings können Unternehmen alternative Lösungswege simulieren und erkennen, welche Variante die effizienteste wäre, wenn zum Beispiel Mitarbeitende in der Kommissionierung krankheitsbedingt ausfallen oder sich aufgrund veränderter Marktbedingungen die Auftragsstrukturen massiv ändern. Ein weiterer Leistungsbaustein ist die Optimierung der Wartungsstrategie in Richtung Predictive Maintenance. Durch die KI-gestützte Auswertung der Nutzungsdaten der Anlagenkomponenten wird das optimale Wartungsfenster ermittelt.
Wie KI den Materialfluss revolutioniert
„Maschinelles Lernen und neuronale Netze werden das Lager leistungsfähiger machen. Der Warendurchsatz steigt, manuelle und automatisierte Flotten lassen sich optimieren, das Personal effizienter einsetzen. Unter dem Strich führt das zu deutlichen Kostenersparnissen für die Unternehmen“, stellt Ulrike Just, Mitglied der Geschäftsführung von Linde MH, in Aussicht. Bei der Strategie von Linde MH geht es in einem ersten Schritt darum, manuelle Flurförderzeuge zu vernetzen. Dafür entwickelt der Intralogistiker aktuell ein System zur Echtzeitlokalisierung, das sowohl innerhalb von Lagerhallen als auch außerhalb von Gebäuden funktioniert. Es ermöglicht die lückenlose Standortverfolgung eines jeden Fahrzeugs und nutzt dafür die low infrastructure-Ultra-Breitband-Technologie. Über ein intelligentes Display erhalten die Fahrer Anweisungen zur Navigation durch das Lager oder bekommen neue beziehungsweise geänderte Fahraufträge mitgeteilt. Dabei kombiniert das System Standort- mit Fahrzeugdaten, wie den Lenkwinkel. Auf diese Weise kann die Route in Echtzeit angepasst werden, wenn beispielsweise an Fahrwegen zu viel Verkehr und damit Zeitverlust entstehen sollte.
Digitaler Zwilling des Lagers
Im zweiten Schritt will Linde MH eine abgestimmte Zusammenarbeit und Routenoptimierung zwischen manuellen und automatisierten Flurförderzeugen ermöglichen. „Wenn 100 oder mehr Fahrzeuge koordiniert werden sollen, gelingt das nur mit einer übergeordneten Intelligenz und einer Hardware, die derart große Datenmengen verarbeiten kann“, erklärt Ron Winkler, Managing Director der Digital Business Unit von Linde MH. „Hier kommt die KI der Nvidia Omniverse-Plattform ins Spiel. Es wird ein digitaler Zwilling des Lagers aufgebaut, ein virtuelles 1:1-Abbild der physischen Realität.“ In diesem digitalen Zwilling lassen sich in Sekundenbruchteilen Simulationen rechnen. Entweder zur Optimierung von Fahrwegen und zur optimalen Koordination von autonomen mobilen Robotern (AMRs) sowie manuellen Flurförderzeugen oder um Optimierungen in bestehenden Lagerlayouts zu erzielen.
Lösungsmöglichkeiten für sich ändernde Anforderungen oder Probleme im Lager, wie aktuelle Auftrags- oder Bestandsänderungen, Verkehrsdichte in bestimmten Lagerbereichen, Hindernisse oder überhängende Lasten, werden in Echtzeit erfasst, im digitalen Zwilling simuliert und Neuberechnungen werden zurück an die Fahrzeugsteuerung gespielt – beispielsweise, dass ein verspätet ankommender Lkw vom nächstgelegenen Stapler mit entsprechender Ausstattung entladen werden soll. Dazu sind in der Omniverse-Plattform alle physischen Daten von Flurförderzeugen (zum Beispiel Motorleistung, Lenkwinkel) sowie der Infrastruktur (zum Beispiel Regalplätze, Fahrwege, Maschinenzeiten) digital hinterlegt. In diesem virtuellen Raum werden dann die Informationen verarbeitet, die permanent aus Sensoren, intelligenten Fahrzeug- und Infrastrukturkameras, Lagerverwaltungssoftware und Fahrzeugsteuerungen kommen.